takai
Well-Known Member
Following on from my thread below (which upon re-reading made little sense) I present the destructive investigation of a KK one way / check valve.
I had a chat with Juri at KK when i was getting a new CO2 cylinder and asked him the same question, but he wasnt sure on the design of the check valves either. I had a suspicion it was just a ball bearing in a sleeve that sealed under pressure, and mentioned that I couldnt check without destroying one. He happily volunteered a candidate for destructive testing as they had some old ones that had an 8mm nipple on them rather than the newer 6mm nipples. Thanks goes to KK for the donation of this poor fella... lets call him Bob.
When i got Bob home his nipple was easily stripped off and the ball valve actuation arm removed. However, his ball valve (now now) was less cooperative and required drilling out to remove:
*note* if you are drilling one of these out then absolutely wear eye protection the ball is hardened and tends to fracture rather than cutting cleanly.
With Bobs ball removed it was easy to see the other nylon seat that seals up the other side:
I figured i could drive out the innards with a drift, but I wanted to see if there was any channeling inside the chamber to allow for pressure equalisation, so i chopped Bob in half... sorry Bob.
Unfortunately in this process Bob's smaller ball (after all he isn't Hitler) skittered away across the bench when the end cap ejected itself:
We can see from Bob's autopsy that he a pretty simple affair using just a spring to hold the (missing) ball bearing against the end seat (silver):
The spring is a pretty basic unit with barely any compressive force and so should crack quite easily under 1psi or so. However, this also means that under situations of almost equal pressure between the manifold and the keg you can have the ball floating in the chamber with only minimal pressure holding it against the seat. This ball bearing on aluminium seat contact isn't overly pressure tight and so will bleed pressure backwards across the check valve if the pressure differential isn't high enough.
I think this is what is leading to my kegs slowly depressurising as the SodaStream very slowly bleeds the CO2 in the system (after i have turned off the CO2 cylinder) and this slow change in pressure is enough to bleed out two of the kegs on the manifold (strangely the third remains sealed).
There are better designs than this around, but this will be the way the majority of check valves work, and so it is imperative to keep pressure on both sides of the valve or bleed the manifold entirely.
Thoughts on possible solutions?
I had a chat with Juri at KK when i was getting a new CO2 cylinder and asked him the same question, but he wasnt sure on the design of the check valves either. I had a suspicion it was just a ball bearing in a sleeve that sealed under pressure, and mentioned that I couldnt check without destroying one. He happily volunteered a candidate for destructive testing as they had some old ones that had an 8mm nipple on them rather than the newer 6mm nipples. Thanks goes to KK for the donation of this poor fella... lets call him Bob.
When i got Bob home his nipple was easily stripped off and the ball valve actuation arm removed. However, his ball valve (now now) was less cooperative and required drilling out to remove:
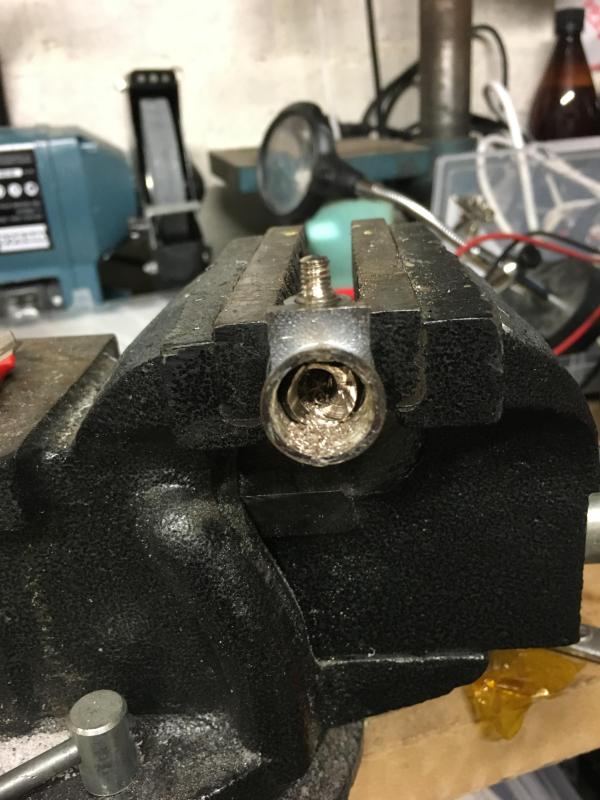
*note* if you are drilling one of these out then absolutely wear eye protection the ball is hardened and tends to fracture rather than cutting cleanly.
With Bobs ball removed it was easy to see the other nylon seat that seals up the other side:
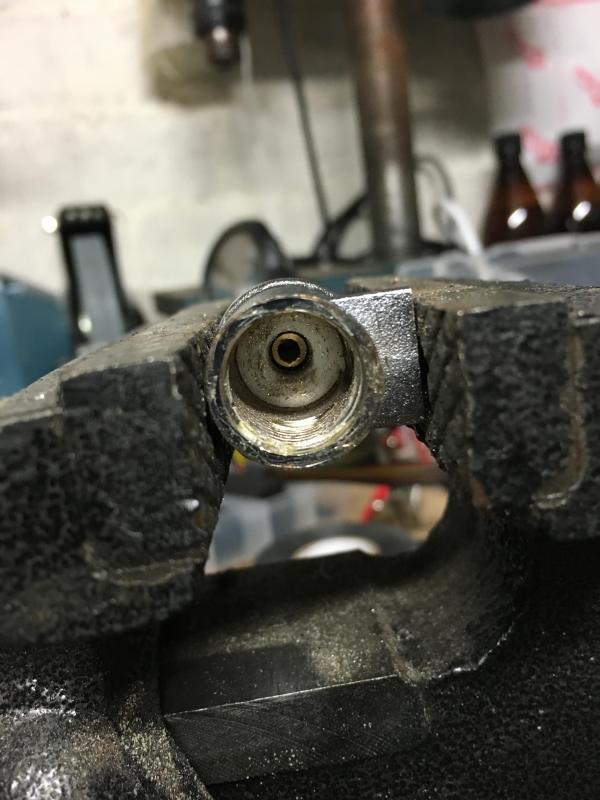
I figured i could drive out the innards with a drift, but I wanted to see if there was any channeling inside the chamber to allow for pressure equalisation, so i chopped Bob in half... sorry Bob.
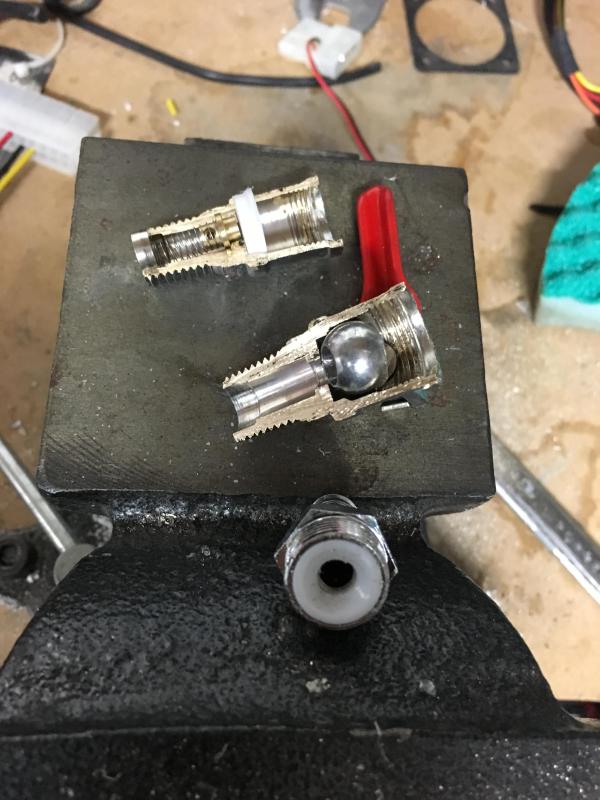
Unfortunately in this process Bob's smaller ball (after all he isn't Hitler) skittered away across the bench when the end cap ejected itself:
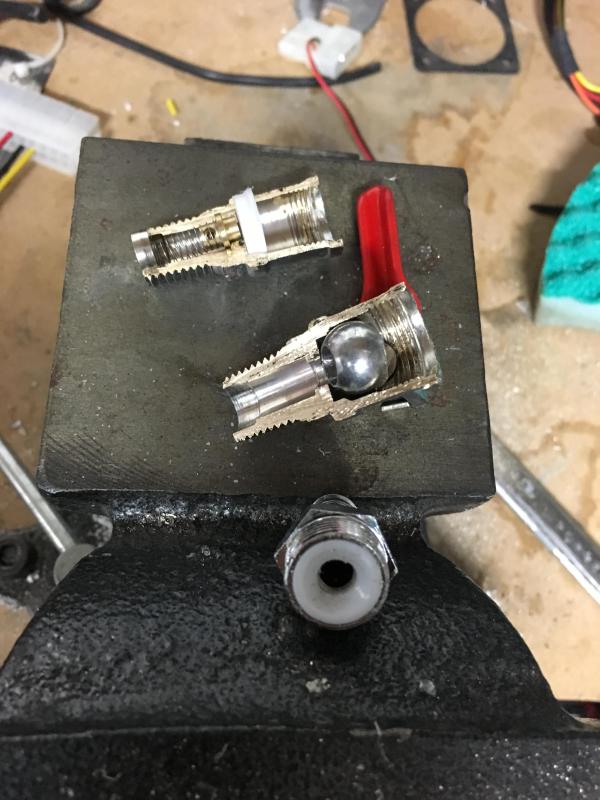
We can see from Bob's autopsy that he a pretty simple affair using just a spring to hold the (missing) ball bearing against the end seat (silver):
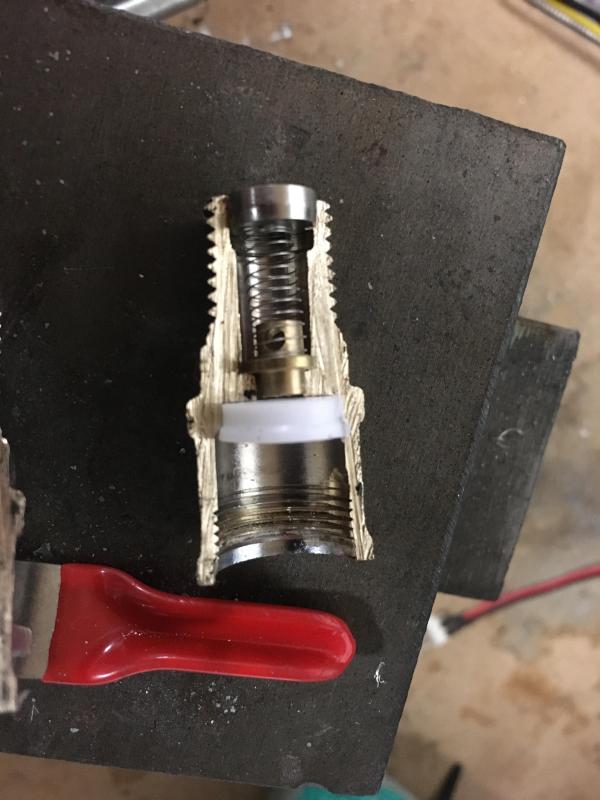
The spring is a pretty basic unit with barely any compressive force and so should crack quite easily under 1psi or so. However, this also means that under situations of almost equal pressure between the manifold and the keg you can have the ball floating in the chamber with only minimal pressure holding it against the seat. This ball bearing on aluminium seat contact isn't overly pressure tight and so will bleed pressure backwards across the check valve if the pressure differential isn't high enough.
I think this is what is leading to my kegs slowly depressurising as the SodaStream very slowly bleeds the CO2 in the system (after i have turned off the CO2 cylinder) and this slow change in pressure is enough to bleed out two of the kegs on the manifold (strangely the third remains sealed).
There are better designs than this around, but this will be the way the majority of check valves work, and so it is imperative to keep pressure on both sides of the valve or bleed the manifold entirely.
Thoughts on possible solutions?